The Role of Plastic Mold Injection Companies in Today’s Manufacturing Industry
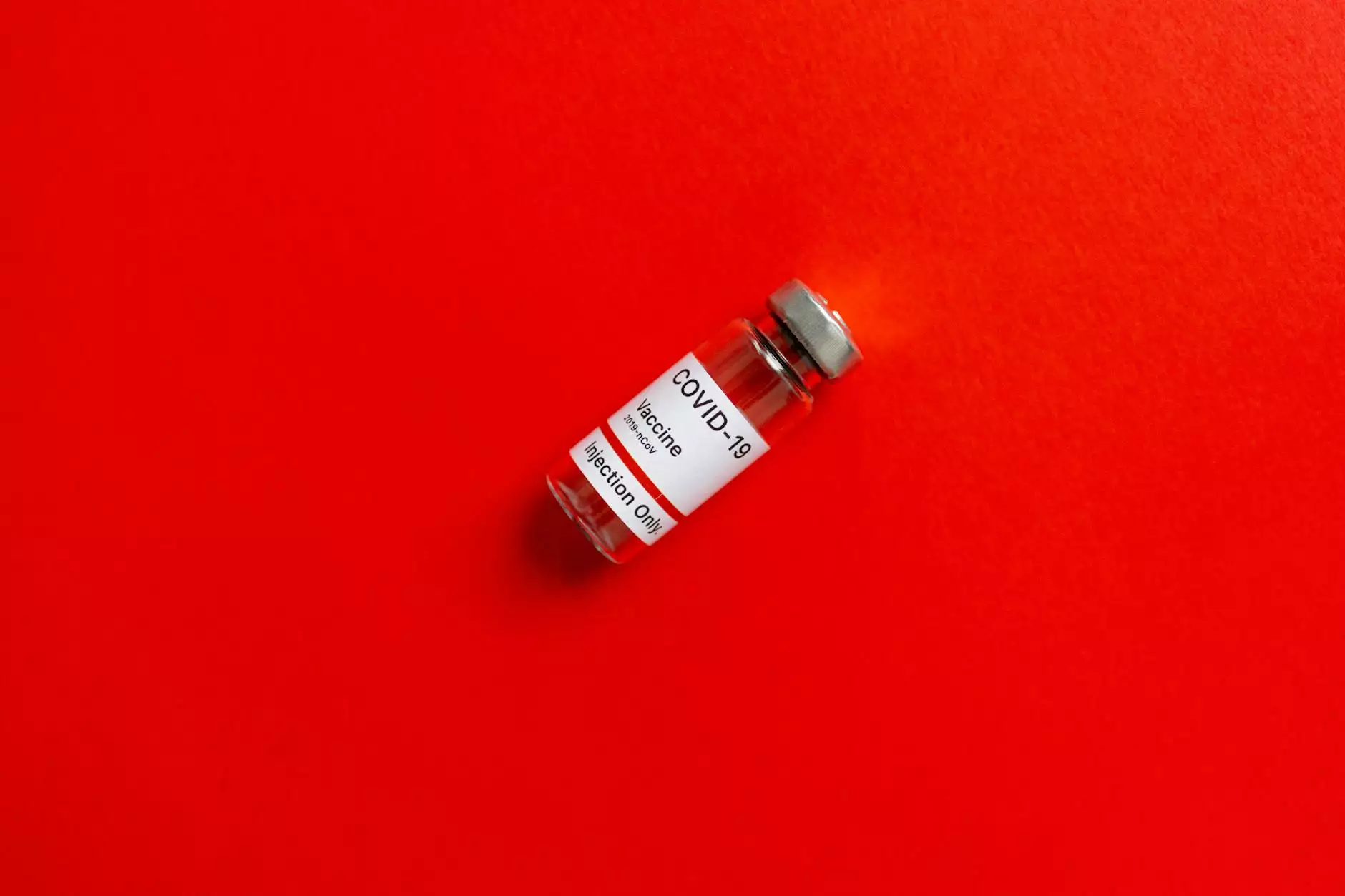
In the fast-paced world of manufacturing, plastic mold injection companies play a crucial role in streamlining production, reducing costs, and fostering innovation. This article delves into the intricacies of the plastic injection molding process, explores the advantages offered by these companies, and discusses their significance in various industries.
What is Plastic Injection Molding?
Plastic injection molding is a manufacturing process used to produce parts by injecting molten material into a mold. The process is ideal for creating complex shapes and is widely used for mass production of plastic components. The main steps involved include:
- Clamping: The mold is clamped shut by a machine.
- Injection: Molten plastic is injected into the mold under high pressure.
- Cooling: The plastic is allowed to cool and solidify.
- Ejection: The mold is opened, and the finished part is ejected.
Types of Plastics Used in Injection Molding
Different types of plastics are employed based on the desired characteristics of the final product. Common plastics include:
- Polypropylene (PP): Known for its elasticity and resistance to fatigue.
- Polyethylene (PE): Offers excellent chemical resistance and is used for many consumer products.
- Polyvinyl Chloride (PVC): Used for pipes and fittings due to its durability.
- Polystyrene (PS): Widely used for packaging and disposable cutlery.
- ABS (Acrylonitrile Butadiene Styrene): Popular for its impact resistance and toughness.
The Advantages of Working with Plastic Mold Injection Companies
Collaborating with reputable plastic mold injection companies offers numerous benefits, which include:
1. Efficiency in Production
Injection molding is designed for high-volume production, allowing companies to manufacture large quantities of parts quickly. By leveraging advanced machinery and automated processes, these companies can significantly reduce lead times and increase output.
2. Cost-Effectiveness
While the initial cost of creating a mold may be high, the per-unit cost decreases as production volume increases. This scalability makes injection molding a cost-effective solution for mass production. Additionally, reduced waste and lower energy consumption contribute to overall cost savings.
3. Precision and Quality
Modern injection molding machines deliver exceptional precision, allowing for tight tolerances and high-quality finishes. This level of accuracy is crucial for industries such as automotive and medical devices, where even minor deviations can lead to significant issues.
4. Material Versatility
Plastic mold injection companies can work with a wide variety of materials, allowing clients to choose options that best suit their product needs. This flexibility enables the production of parts with diverse physical characteristics, enhancing product performance.
5. Rapid Prototyping
Many plastic mold injection companies offer rapid prototyping services, allowing clients to test designs and functionality before committing to mass production. This service helps identify potential design improvements early in the process, saving time and resources.
Industries Benefiting from Plastic Injection Molding
Plastic injection molding finds applications across a myriad of industries, including:
1. Automotive Industry
The automotive sector heavily relies on injection molding for producing components such as dashboard parts, interior trims, and under-the-hood applications. By utilizing lightweight and durable plastics, manufacturers can contribute to improved fuel efficiency.
2. Medical Devices
In the healthcare field, strict regulations demand precision and biocompatibility. Plastic mold injection companies provide critical manufacturing solutions for medical devices, equipment housings, and disposable tools.
3. Consumer Products
From household items like containers and toys to more complex electronics, the consumer goods sector benefits immensely from injection molding. The ability to customize designs encourages innovation while keeping production costs manageable.
4. Electronics
With the growing demand for electronic devices, the need for high-quality plastic components has surged. Injection molding is instrumental in producing casings, switchgear, and other protective components for electronic products.
5. Aerospace and Defense
This sector requires robust materials that can withstand extreme conditions. Plastic injection molded parts are increasingly used in aerospace applications, contributing to weight reduction and performance enhancement.
Choosing the Right Plastic Mold Injection Company
When selecting a plastic mold injection company, it is crucial to consider several factors to ensure you partner with an organization that aligns with your needs:
1. Experience and Reputation
Opt for companies with a proven track record in the industry. Research their history, client testimonials, and case studies to gauge their ability to deliver quality results.
2. Technological Capabilities
Advanced machinery and technology are fundamental for precision and efficiency. Ensure that the company invests in state-of-the-art equipment that can handle your project’s specific requirements.
3. Material Expertise
Choose a supplier with extensive knowledge of various materials and their properties. This expertise can help you make informed decisions about which plastics to use for your application.
4. Customization Options
Look for companies that offer customized solutions to meet your unique project specifications. Whether it’s altering mold design or adapting production techniques, flexibility is key to successful collaboration.
5. Maintenance and Support
Consider suppliers that provide ongoing support and maintenance for their products. A reliable partner will assist you throughout the entire production process and beyond.
The Future of Plastic Injection Molding
As technology continues to advance, the future of plastic injection molding looks promising. Innovations such as:
- 3D Printing Integration: The combination of 3D printing and injection molding could revolutionize prototyping and production.
- Biodegradable Plastics: The rise of eco-friendly materials is paving the way for sustainable manufacturing practices.
- Smart Manufacturing: IoT integration will enhance automation and monitoring in the injection molding process.
With these advancements, plastic mold injection companies will not only maintain their pivotal role in manufacturing but also evolve to meet the challenges of the future. The adaptability of this industry to incorporate technological innovations ensures its longevity and relevance.
Conclusion
In summary, plastic mold injection companies are indispensable to modern manufacturing, offering unmatched efficiency, cost savings, and precision across various industries. By understanding the nuances of injection molding and choosing the right partner, businesses can unlock significant potential in their product development processes. The journey of innovation and excellence in plastic injection molding is ongoing, and those who embrace it can secure a competitive advantage in their respective markets.
For more information about advanced injection molding solutions, visit deepmould.net and discover how we can help you elevate your manufacturing processes.