Understanding China Plastic Injection Molding: A Gateway to Quality Manufacturing
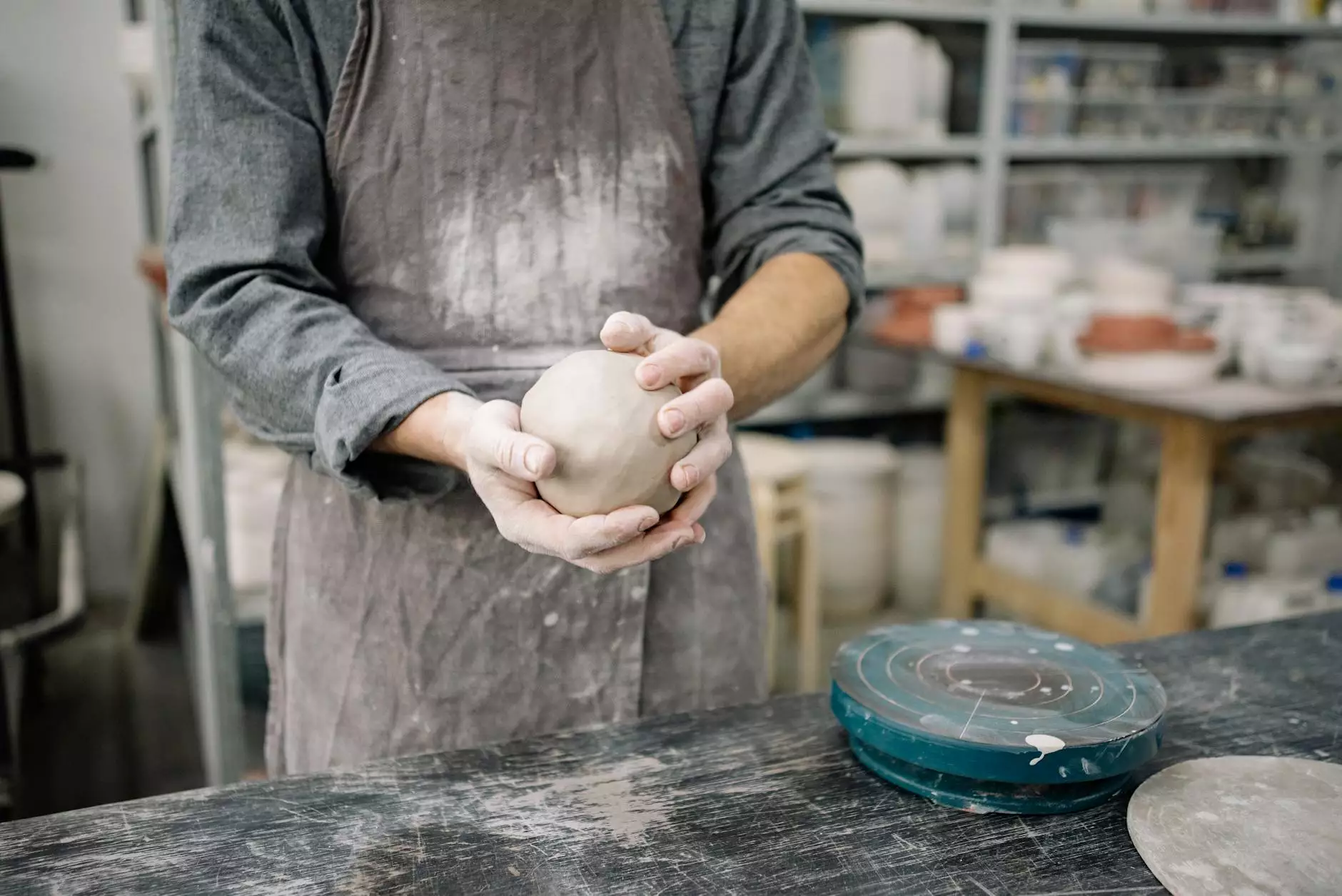
China plastic injection molding has emerged as a pivotal manufacturing process, enabling businesses worldwide to produce intricate and high-quality plastic components. This article delves into the essentials of plastic injection molding, explores its advantages, and illustrates how it transforms supply chains, particularly in the realm of metal fabrication.
The Fundamentals of Plastic Injection Molding
At its core, plastic injection molding is a process where molten plastic is injected into a mold to form various products. This technique is renowned for its efficiency and ability to produce precise, repeatable parts.
How the Process Works
The injection molding process can be broken down into five essential steps:
- Material Preparation: The process begins with the reception of plastic resin pellets, which are selected based on the desired properties of the final product.
- Heating: The plastic pellets are fed into a hopper, where they are heated until they become molten.
- Injection: The molten plastic is then injected into a mold at high pressure.
- Cooling: The injected plastic is allowed to cool and solidify within the mold.
- Ejection: Once the plastic has cooled sufficiently, the mold opens and the finished product is ejected.
The Advantages of Choosing China for Plastic Injection Molding
Businesses globally are increasingly turning to China for their plastic injection molding needs due to several compelling factors:
- Cost-Effectiveness: Manufacturing costs in China are generally lower due to reduced labor and operational costs. This allows businesses to save significantly on production.
- Advanced Technology: Chinese manufacturers are continuously upgrading their technology and capabilities, ensuring high-quality output.
- Scalability: Chinese facilities are equipped to handle projects of any scale, from small prototype runs to mass production.
- Expertise and Experience: With decades in manufacturing, Chinese companies offer extensive experience in various sectors, including automotive, electronics, and consumer goods.
Applications of Plastic Injection Molding in Modern Industry
The versatility of china plastic injection molding allows it to cater to a wide range of industries, each with unique requirements and challenges:
1. Automotive Industry
In the automotive sector, precision and durability are paramount. Plastic injection molding is used to create components such as dashboards, housing for electronics, and even parts for engines.
2. Consumer Electronics
With the increasing demand for lightweight and complex designs, consumer electronics manufacturers rely on injection molding to produce enclosures, connectors, and other integral components.
3. Medical Devices
In the medical field, hygienic and precise components are critical. Plastic injection molding allows for the production of items like syringes, canisters, and instrument casings that meet stringent regulatory standards.
4. Packaging
Plastic injection molding produces durable and lightweight packaging solutions that are both functional and environmentally friendly. Think of containers, lids, and dispensers that require consistency and durability.
The Role of Metal Fabricators in Enhancing Injection Molding
While plastic injection molding is a remarkable process on its own, the interaction with metal fabricators can amplify its effectiveness. Metal fabricators play a crucial role in producing the molds needed for injection molding.
Collaboration with Metal Fabricators
By collaborating with expert metal fabricators, businesses can ensure that their molds are:
- Durable: High-quality molds provide long-term reliability.
- Precise: Meticulous craftsmanship ensures parts come out as designed.
- Cost-Effective: Well-made molds reduce the need for repairs or replacements, improving ROI.
Innovations in Metal Fabrication for Molds
Recent advancements in metal fabrication techniques, such as CNC machining and 3D printing, have enabled the production of complex molds that were previously unattainable. These innovations facilitate rapid prototyping and shorter timelines for manufacturers.
Quality Control in the Injection Molding Process
Ensuring the quality of molded parts is integral to maintaining customer satisfaction. This is particularly where the synergy between china plastic injection molding and rigorous quality control measures comes into play.
Best Practices for Quality Assurance
- Regular Inspections: Conduct frequent inspections of both the molds and the final products to identify and rectify issues early.
- Statistical Process Control: Utilize data analytics to monitor the injection molding process in real time, helping to maintain standards.
- Prototype Testing: Before mass production, prototypes should be created for testing to ensure the design meets specifications.
The Future of Plastic Injection Molding in China
As the manufacturing landscape evolves, china plastic injection molding is poised for significant advancements. Several trends are shaping its future:
1. Sustainability Initiatives
With increasing regulatory and consumer pressure for sustainable practices, Chinese manufacturers are focusing on eco-friendly materials and processes. This shift towards sustainability can enhance brand image and meet global market demands.
2. Automation and Smart Manufacturing
Automation and Industry 4.0 technologies are being integrated into the injection molding process, leading to increased efficiency, reduced waste, and improved product quality. This tech-savvy approach will redefine production capabilities.
3. Customization and Rapid Prototyping
The demand for customized products is rising, driven by consumer preferences. Enhanced prototyping techniques will enable quicker iterations and a more responsive production approach to meet diverse customer needs.
Choosing the Right Partner for China Plastic Injection Molding
Selecting the right injection molding partner is crucial for business success. Consider the following criteria when choosing a manufacturer:
- Reputation: Research potential partners thoroughly; check reviews and case studies.
- Certifications: Ensure they meet international quality standards.
- Communication: Effective communication channels are essential for project transparency and timely execution.
Conclusion
Given its numerous advantages, china plastic injection molding stands out as a premier manufacturing choice for businesses looking to thrive in an ever-competitive marketplace. By leveraging cutting-edge technology, skilled metal fabricators, and robust quality control systems, companies can significantly enhance their production processes and outcomes.
Whether you’re in the automotive, electronics, or any other industry requiring precise and durable plastic components, partnering with an experienced and innovative injection molding provider can create pathways to success.